2問題解決のための手法
問題解決のロジックツリー
ロジックツリーとは、MECE(「モレ」なし・「ダブリ」なし)の考え方を使って、上位概念を下位概念にツリー状に論理的に分解するものです。ロジックツリーには、①問題の原因を追求する、②問題の解決策(およびその代替案)を考える、という2つの活用法があります。
原因追求のロジックツリー
正しい解決策を導くためには、起こっている問題の原因を徹底的に追究しなければなりません。「なぜ?」と繰り返しながら、より深く追求し、本質的な原因を究明することが重要です。
そして、もう一つ重要なことは、MECEで考えることです。ロジックツリーでは、どんどん原因を掘り下げていく「縦の関係」と、ツリーの各階層の広がりという「ヨコの関係」があります。この横の関係において、モレ、ダブリ、ズレがないように広がりを考えなければなりません。
問題解決のロジックツリー
ロジックツリーのもう一つの活用法として、解決策を考えることがあります。ロジックツリーを使って問題の解決を導くためには、「So How?(それでどうする?)」を繰り返す必要があります。前述の例では、「シェアの低下」まで原因を追究しましたが、このようにいくら深く原因を追究しても、「シェアを増加させろ」では、単なる問題の裏返しの解決策になってしまいます。課題に対して、ある解決策を出したならば、その解決策に対して「それでどうする?」と自分に問いかけ、さらなる具体的な解決策を出していきます。
A社のシェア低下は、A社のライバルである業界1位のB社のシェア拡大によるものだとします。このとき、A社としては、B社に奪われた分のシェアを回復し売上数量の回復⇒利益の回復を目指すことになります。そのためにはどのような解決策を取ったらよいか考えてみました。まず、シェアを回復する手段として、以下の3つの解決策を考えました。①新しい分野に進出し直接対決を避ける ②堂々と同じ土俵で直接対決をする ③弱いものいじめをする
この3つの中からどれが解決策としてふさわしいかを判断するために、自社とB社の比較などを分析するわけですが、ここでは仮に②の解決策をさらに"So How"してみます。製品で差別化するか、低価格で勝負か、攻撃的なCMを打つかなど、解決策を具体化していきます。
ここでもう一つ重要なことは、その具体策をアクションに移さなければ、全く意味がありません。「実現可能である」という命題を自分の頭のロジックに組み込んで、具体的解決策を考えることが必要です。
パレート分析
パレート分析とは
パレート分析は、イタリアの科学者パレートの名に由来するもので、全体の結果に対して貢献度の高い(影響度の大きい)要素の集中度やその隔たりを見るものです。経験則上、アウトプットの80%は、わずか20%のインプットから得られるという関係が成り立つため、「20-80の法則」とも言われます。
たとえば、営業マンの業績においては常にバラツキが生じ、結果として売上や利益に貢献するのは全営業マンの20%ということが起きます。そこで、成績が中~下位の営業マンのボトムアップを図るべきか、成績上位の営業マンをさらにスーパー営業マン化を図るべきかということが論点となります。
この場合、すでに高業績を残している営業マンにさらに負荷をかけるよりも、業績が中~下位のボトムアップを図った方がより効果的であるといえます。
また、企業で取り扱っている商品に目を向けても、同様の傾向が見られます。下図は、ある家具メーカーにおける机の売上集中度ですが、この自社では定番商品のほかに、取引先の要望に応じて製造する特注タイプの机を生産しています。取引先の要望という理由で特注品を増やしていますが、手間がかかる割に売上は伸びず、収益には貢献していないことがわかります。
パレート分析の活用
パレート分析は、均一になりがちな資源、商品、営業マン、顧客の取り扱いを、その貢献度に応じて「差別化する」ことにその意味があり、以下の3点が考えられます。
①高貢献度群の維持
貢献度の高い商品や顧客へさらに資源を投入し、生産性や満足度を高める。
②低貢献度群の改善
現状は貢献度が低いが、将来ポテンシャルのある商品や顧客を見極めて資源を投入し、収益性を改善する。
③低貢献度群の整理
貢献度の低い商品や顧客を見極めて整理する。
①の方法は、顧客であれば上位客として、さらにキメの細かいサービスを提供することで良い関係を保ち、他社に奪われないようにすべきということです。
②の方法は、高貢献度群の裾野を広げるという意味では重要ですが、実践には工夫が必要です。なぜ貢献度が低いのかをよく分析して、どれほど資源を投下すれば貢献度が上がるのか、その可能性を予測する必要があります。大事なことは情報を良く集め、改善目標を定めてモニタリングし、一定期間における達成度で判断することです。
最も注意すべきなのは③の方法です。理論的には「不採算=整理」という考えが成り立ちますが、むやみに実行した場合のリスクも大きくなります。不採算部門を整理したら、かえって赤字が増えたということもあり得ます。
したがって、これらの構成要素の一つひとつについてを個別に判断しなければなりません。
【構成要素の個別判断項目】
- 粗利益以外の指標で見た場合はどうか
- 過去の動きはどうであったか、また今度はどうなりそうか
- たとえば商品ラインのように、低貢献度群に含まれていても高貢献度群の商品とラインアップしてシナジー効果がないか
粗利益では貢献していない顧客でも、人的ネットワークが広く、多くの上客を紹介してくれるかもしれないからです。
ABC分析
ABC分析は、パレート図を活用して、資源配分を適正に行なうために、重点分野をABC・・・とランキングして優先順位を明らかにするものです。商品や顧客を売上高や利益貢献度の高い順にランキングして、低ランクのものを整理する方法です。
販売管理を例にABC分析の活用の仕方を以下に示します。
(1)ABC分析の作成方法
パレート図を利用して左から順にA、B、Cランクに区分けします。
ABCランクの基準値は、
- A:累計比68~70%
- B:累計比90(95)%まで
- C:90(95)~100%
対角線を引いて(左下の0基点から右上へ)、対角線とパレート曲線に囲まれた部分の面積で、ランクの集中度がわかります。(例:Aランク部分が広いほど、上位集中型)
(2)集中管理
通常、グラフは急カーブを描くため、Aランクの占める割合が大きいケースが大半を占めます。Aランク顧客は自社に対する貢献度、重要度が高いため、集中管理を行ないます。たとえば、営業訪問回数の累積比を訪問先ごとにインプットし、できるだけパレート曲線に近い訪問割合として重点管理を行います。
(3)層別管理
Aランクが経営上の問題で、取引できなくなるケースを想定し、BランクからAランクに引き上げることができる顧客を想定します。Bランクが少ない場合、Cランクからの引き上げを図ります。Cランクについては、現状維持か整理(切り捨て)も考えます。攻める顧客、守る顧客、整理する顧客の選択整理に役立ちます。
顧客管理以外にも、商品別管理、営業所別管理など様々な管理に活用できます。
特性要因図
特性要因図とは
特性要因図は、その問題にどのような原因があるのかを探るための技法で、収束技法のひとつです。「特性要因」とは、「問題を引き起こしている原因」を指します。つまり、問題がどのような要因(原因)で起きているかを図解化(特性要因図)し、問題点を把握していく手法です。図の形から「魚の骨(フィッシュボーン・ダイアグラム)」とも呼ばれます。
一つの結果(特性)にはあらゆる原因があります。特性要因図はこれらの原因を追究する場合に活用したり(原因追求型特性要因図)、特性要因図を用いると、要因(原因)の因果関係が一目瞭然となることから、管理や改善のやり方の検討に用いたりします(対策検討型特性要因図)。
特性要因図の作成方法
特性要因図は以下の手順で作成していきます。
●特性(問題)を決める
特性と背骨を書く
●特性の要因(原因)を洗い出す
大骨を入れる
●さらに要因(原因)を分解する
中骨、小骨を入れるく
●要因(原因)の重み付けを行なう
(1)特性(問題)を決める
まず、問題とする特性を決め、背骨を書きます。特性を決めるときには、データの得やすい特性であること、改善効果の大きい特性から手掛けることがポイントです。
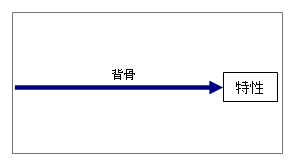
(2)特性の要因(原因)を洗い出す
ブレーンストーミングなどを活用して、特性の原因を挙げます。これらの原因を層別した一番上のレベル(大分類)を要因といい、背骨に向かって斜めに大骨を入れます。
大骨の大分類には、人・機械・材料・方法のほか、作業環境や・検査方法などがあります。
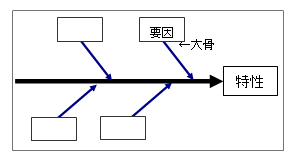
(3)さらに要因(原因)を分解する
大骨だけでは、要因(原因)の対象が大きすぎて対策を取ることができません。そこで大骨に対して中骨・小骨と原因を分解して付帯的な対策が取れるレベルまで分解していきます。そのためには、「なぜ?」を繰り返し、意見が出なくなるまで繰り返します。

(4)要因の重み付けを行なう
検討した要因のうち、どの要因から調べていくかを明確にするため、影響度の大きいと思われる要因を調べ、枠で囲むか、色で明確になるようにして要因の重み付けを行います。影響度が数値で表せる場合は、パレート図にて影響度の大きい2、3項目に印を付けます。影響度が数値で表せない場合は、再度ブレーン・ストーミングを行ない、影響度の大きいと思われる要因を調べ、印を付けます。
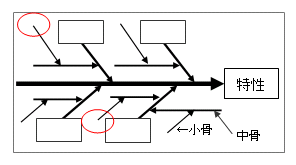
特性要因図の例
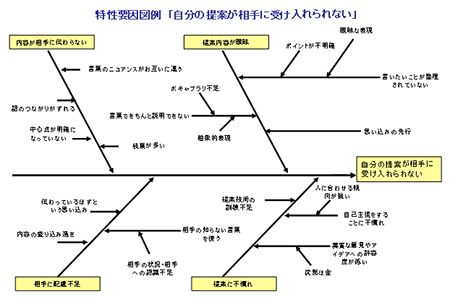
作成した特性要因図を点検する
作成した特性要因図を見ながら、次のような確認を行います。
- 特性は目的に合った(原因追求型か対策検討型)表現になっているか
- 大骨から小骨まで、系統立てられて整理されているか
- 特性に関係のない原因が入っていないか
- 原因の重み付けと優先順位が決まっているか
- 末端の原因について具体的な行動を取れる所まで検討されているか
- 原因の追求に漏れがないか
グラフ
グラフとは
グラフは、数値を図形にして大きさを比較したり、過去・現在・未来に対する状態など、データを視覚化してわかりやすくしたものです。グラフ化することで、表などとは異なり、視覚から数値の大小や推移を確認することができます。
また、グラフは、項目別の比較をするとき、提案件数、不良率の推移を見るときなど様々な場面で活用できます。
グラフの種類と用途
①棒グラフ
データの大小を比較する場合
②折れ線グラフ
時間の経過を追うデータや、変化や傾向をつかみたい場合
③円グラフ
数値の大小よりも、占有率に意味がある場合
④レーダーチャート
いくつかの項目のバランスを見たい場合
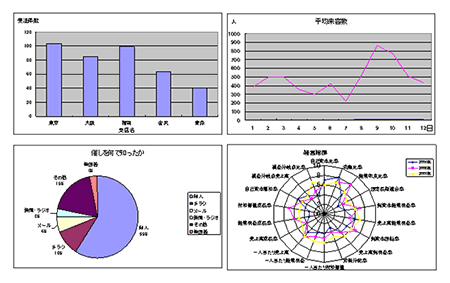
チェックシート
チェックシートとは
チェックシートは、データを分類項目別に見やすく表したものです。問題解決においては、チェックシートはデータとして使用されます。各種データは集計し、各種グラフなどで表されます。ここで、現状の把握や要因の解析などを行うことで、問題点の明確化や原因解明へと結び付けます。チェックシートには決まったフォームはありませんが、層別を考慮し記入しやすい形でまとめます。
効果的なチェックができるばかりでなく、データの集計・整理をしやすいフォーマットの記録用シートです。チェックシートは、目的、職場や仕事よっていろいろ工夫して作られ、非常に数多くの種類があります。
分布の状態や欠点・不良項目が、どこにどのくらい発生しているかを調査するために用いたり、点検すべき項目をあらかじめ決めておいて、点検作業を容易に確実に行うために用いたりします。チェックシートは、層別データの記録用紙として用いて、パレート図及び特性要因図のような技法に使用できるデータを提供することもできます。また、チェックシートは作業の点検漏れを防止するためにも使用できます。
チェックシート作成のポイント
- データの分類項目とそれに見合った記録用紙の形式を決定する
- データを収集・マーキングする
- 所定事項(目的、データ数、期間、作成者など)を記入す
ヒストグラム
ヒストグラムとは
ヒストグラムは、計数値の存在する範囲をいくつかの区間に分け、各区間に入るデータの出現を表す度数表を作り、横軸に特性値、縦軸に度数を目盛り、各区間に属する度数を柱の高さで表し、柱状図にしたものです(度数分布図ともいわれます)。
一般に、ある特性を測定して得られるデータの度数は、ある値を中心に分布を持っています。このデータから、集団として品物の性質を知るために、測定データを統計的に解析して、分布の状態を見やすくすることが必要となります。このためにヒストグラムとして表され、その分布状況によって、工程の異常や不良品発生傾向を知ることができます。データの中心傾向(平均値、メジアン、モード)によって、規格、標準値の適合状態を確認したり、バラツキや偏りを把握します。
ヒストグラムの作成手順と見方
(1)ヒストグラムの作成手順
ヒストグラムの作成手順は次の通りです。
- aデータを集める。
- bデータの最大値と最小値を調べ、最大値と最小値の差(=範囲)を求める。
- c範囲をもとに、区間の数または間隔を設定する。
- d度数分布表を作り、棒グラフを作成する。
- e区間の間隔を変えてみて、データ集団の性質をつかみやすい間隔を選ぶ。
(2)ヒストグラムの見方(チェックポイント)
ヒストグラムは、以下の観点を考慮に入れて評価します。
- ヒストグラムの形状(次ページ参照)
- データのばらつき
- 分布の形
- 企画値との関係
- 分布の中心は規格値の中央にあるか否か
- 規格値よりはみ出していないか(規格値が設定されている場合)
- 規格値の幅の中に余裕を持って入っているか(規格値が設定されている場合)
管理図
管理図とは
管理図は、プロセスが問題なく運用されているかを管理するための手法です。管理図には、中心線と上下一対の管理境界線が引かれており、データをプロットすると、データのばらつきが偶然によるものか、異常によるものかを判断できます。管理図を用いることで、品質不良や工程の異常を察知し、不良原因の除去や再発防止対策をとることができます。
管理図は、工程の状態とその原因をつかめていない場合、ある期間のデータを取り、どこにバラツキがあるか見る「解析用」と、UCL(上方管理限界)、LCL(下方管理限界)を決定する解析や、工程が運用に入った後、データを連続的に採取し、限界線を外れる異常を検出する「管理用」とに、その用途は分かれます。
管理図の種類
管理図には、データの種類によって下記に示すような種類に分類できます。
管理図の作成方法
ここでは、管理図のなかでも最も頻繁に使われるXbar-R管理図の作成方法について解説します。
- 決められた時間ごとに出来上がった製品の中からサンプルを抜き出し、測定値(平均値)をグラフにプロットする。
- 測定点が管理限界外に出たら、直ちに製造工程をストップし、原因を調べ原因排除に努める。
管理図の見方
管理図を見るときは、管理限界だけではなく、全体としての傾向を見る必要があります。
散布図
散布図とは
2種類のデータにおける相互関係を調べるために、一方を横軸に他方を縦軸にとってプロットしたものです。経験年数と不具合件数、年齢と基本給など、対になったデータの相関関係を見る際に使用します。
散布図の見方
- 点の散らばり具合と相関関係
- 外れ値はないか:全体の点の並びから飛び離れた点があれば原因を調べます
- 層別の必要性はないか:全体を見ると相関がありそうだが、層別すると相関がない場合があります。
- 相関の大きさを相関関係で見る
※層別:データを特定のグループに分類してデータの特徴をはっきりさせ整理すること。
層別されたデータはパレート図やヒストグラムで分析します。
上で示した散布図では、年齢が進むにつれて基本給が増加しています。これを「正の相関」といいます。また、下図で示すように、「正の相関」と全く逆の「負の相関」や2種類のデータにまったく相関関係がない場合もあります。